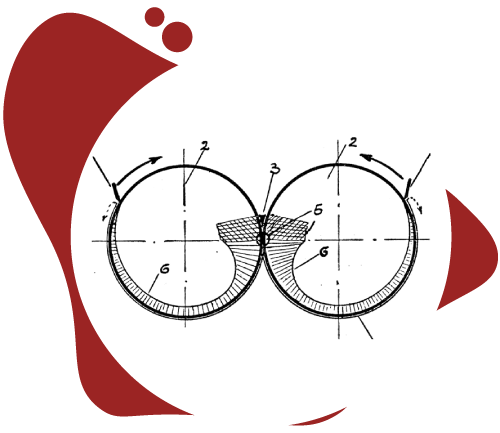
Roller Dryers (Thin Film Dryers) / Drum Coolers
General
Although all kinds of low viscosity products can be processed with the roller dryer, for economic reasons one would want to limit its application to a pre-concentrated product, in a viscous, slurry stiff pasty form. For this purpose, upstream systems for pre-evaporation are expedient.
Operating principle
The operating principle is based on 2 heated or cooled (drum coolers) and counter-rotating rollers, which roll on the product against each other. The product is added from above. The product distributes evenly in the roller gap and is held in the corresponding position with the core components. The rotary movement creates a product film on the rollers. Changes in the roller gap, the rotation speed, circumference and temperature of the rollers, as well as the degree of the vacuum are directly dependent of each other and have a direct impact on the drying speed and the drying result. The knives arranged on both sides remove the dried or cooled, mostly skin-shaped to clumpy product from the roller body. Any potential knife abrasion is actively prevented and does not occur.
Application
- Drying and crystallisation of viscous to stiff pasty, sticky products
- Cooling and solidification of melts and suspensions for the creation of homogenous structures.
Advantages
- Fully-automated processes
- Operation from normal pressure to high vacuum
- Drying is possible both continuously or by batch
- Large maintenance and cleaning openings
- Fully-automated CIP (Cleaning in Place) / SIP (Sterilization in Place), possible
- ATEX, GMP and FDA compliant
- Low electric power requirements thanks to energy recovery
- Compact design, minimal product loss in the machine
- Low cleaning effort, as only the roller surface comes into contact with the product
Disadvantages
- Size limited for construction reasons
Other variations
Single vacuum drum dryer
Atmospheric single / double drum dryer